Our Services
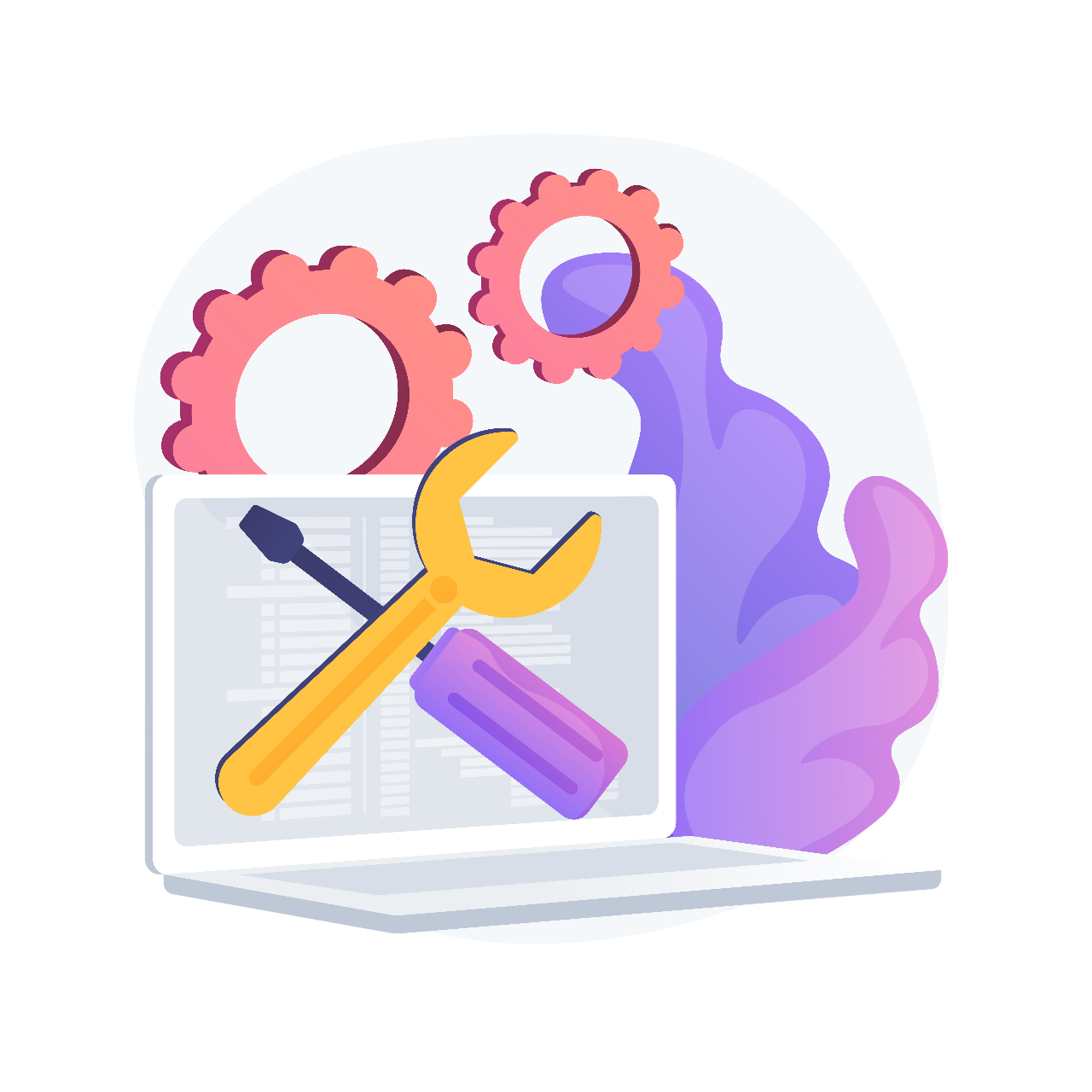
Quality Of Control
Quality Control in Stone Processing
Quality control in building stone processing is a multi-stage process that is carried out to ensure that the final product meets technical, aesthetic, and safety standards. This process includes the following steps:
- Quality control at the extraction stage (Quarrying)
- Initial inspection of the raw stone: Identification of natural defects such as cracks, irregular veins, or color changes.
- Selection of healthy blocks: Use of sonar devices or visual inspection to separate quality blocks.
- Monitoring of environmental conditions: Prevention of damage caused by explosions or improper cutting in the mine.
- Control in the cutting and shaping process
- Dimensional accuracy: Use of world-standard devices such as CNC or waterjet for precise cutting in accordance with engineering designs.
- Cutting of plates: Ensuring uniform thickness, smooth surface, and absence of burrs.
- Color and texture control: Matching the color patterns and texture of the stone with approved samples.
- Surface Treatment
- Polishing and polishing: Checking the level of shine, uniformity of the surface, and the absence of lines or scratches.
- Sandblasting or flaming: Ensuring the uniformity of the texture created on the surface of the stone.
- Antique or chiseling: Controlling the depth and pattern of depressions to maintain the strength of the stone.
- Technical and mechanical tests
- Compressive and flexural strength: Testing according to standards such as ASTM C170 or EN 12372.
- Water absorption: Measuring the permeability of the stone using standard methods (e.g. EN 13755).
- Abrasion: Testing the surface resistance to abrasion (e.g. ASTM C241 standard).
- Frost resistance: Checking the vulnerability of the stone in freeze-thaw cycles.
- Final inspection
- Dimensional compliance: Measuring length, width, thickness, and angles using calipers, laser, or CAD software.
- Visual integrity: Identify stains, color changes, or design inconsistencies.
- Labeling and grading: Separate stones by quality (grade A, B, C, etc.).
- Packaging and transportation
- Use of resistant pallets: Prevent breakage during transportation.
- Edge protection: Use foam or edge bands.
- Humidity and temperature control: Prevent cracking or discoloration in storage or transportation.
- Documentation and standards
- Issuance of quality certificates: Provide documents in accordance with international standards (ISO 9001, CE Marking, etc.).
- Traceability: Record information on each block from the quarry to the installation site to enable follow-up in the event of defects.
- Contributing factors
- Personnel training: Ensure workers are skilled in using equipment and identifying defects.
- Waste management: Recycle cutting waste to reduce costs and pollution.
- Workplace monitoring: Observe occupational health and safety principles in the production line.
By implementing these steps, manufacturers can provide stones with high quality, appropriate strength, and desirable appearance for construction projects.
Transportation
Building Stone Transportation Standards
Building stone transportation standards refer to a set of rules and guidelines developed to maintain the quality, safety, and integrity of the stone during transportation. These standards are designed to prevent physical (fracture, cracking, abrasion) and environmental (humidity, temperature) damage. The most important standards and key points in this area are given below:
- International and National Standards
- ISO 9001 (Quality Management System): Ensuring quality control processes in packaging, loading, and transportation.
- ASTM D5635 (Natural Stone Packaging Standard): Technical specifications for protecting the stone against impact and moisture.
- EN 1469 (European Standard for Natural Stone Installation): Includes safe transportation requirements for stone slabs.
- DIN 51130 (Stone Surface Slip Resistance Test): Related to safety in handling floor stones.
- Transportation Requirements by Type of Vehicle
a) Road Transportation:
- Use of wooden or metal pallets: Stones must be fixed on standard pallets (with appropriate dimensions).
- Load stabilization: Use of steel straps, anti-slip belts, and edge protection foams.
- Waterproof coating: Stones must be covered with moisture-resistant plastics (such as polyethylene).
- Permitted load height: Do not exceed the specified height to prevent overturning.
b) Sea Transportation:
- Use of dry containers: Prevent moisture and salt from penetrating into the packages.
- Fixing pallets in the container: Using restraining sticks (Dunnage) to prevent stones from moving.
- Temperature and humidity control: In case of transporting sensitive stones (such as limestone), use containers equipped with a ventilation system.
c) Rail Transportation:
- Shock and vibration absorption: Use of springs or shock-absorbing layers in the floor of the wagons.
- Dustproof coating: Protect the stone from contamination caused by train movement.
- Packaging Standards
- Edge protection: Use of edge protectors or U-shaped foam.
- Layer separation: Place cardboard or foam layers between the stone sheets to prevent abrasion.
- Labeling: Include warning signs such as “fragile,” “away from moisture,” or “this side up” on the packages.
- Package weight standard: Each package should not weigh more than 1.5 tons to ensure safe transportation.
- Safety and Environmental Requirements
- Loading and unloading: Use of cranes equipped with soft pads or special stone forklifts.
- Avoid manual loading: For stones larger than 30×30 cm, the use of machinery is mandatory.
- Waste management: Recycle used pallets and plastics in accordance with environmental standards (e.g. ISO 14001).
- Documentation and Certificates
- Certificate of Origin: Confirms the origin of the stone for crossing borders.
- Inspection Report: Records the condition of the stone before and after transportation.
- Bill of Lading: Details of the type of stone, weight, dimensions, and transportation conditions.
- Key Points for Safe Transportation
- Avoid storing stones in humid environments: Water-absorbing stones (e.g. travertine) should be stored in a dry environment.
- Control the storage temperature: Avoid freezing or extreme heat that causes cracking.
- Use standard pallets: The height of the pallet should be at least 10 cm from the ground to prevent water ingress.
- Specific Standards for Stone Types
- Marble stones: Requires anti-acid coating and special protection of the polished surface.
- Granite stones: Higher resistance in transportation but requires protection of sharp edges.
- Facade stones (slabs): Vertical transportation to prevent breaking of large plates.
By adhering to these standards, haulage companies that are members of the 3SG network reduce the risk of damage to the stone during transport and maintain the quality of the product until it reaches the final project site. Manufacturers and suppliers should coordinate closely with haulage companies to ensure that these requirements are implemented correctly.